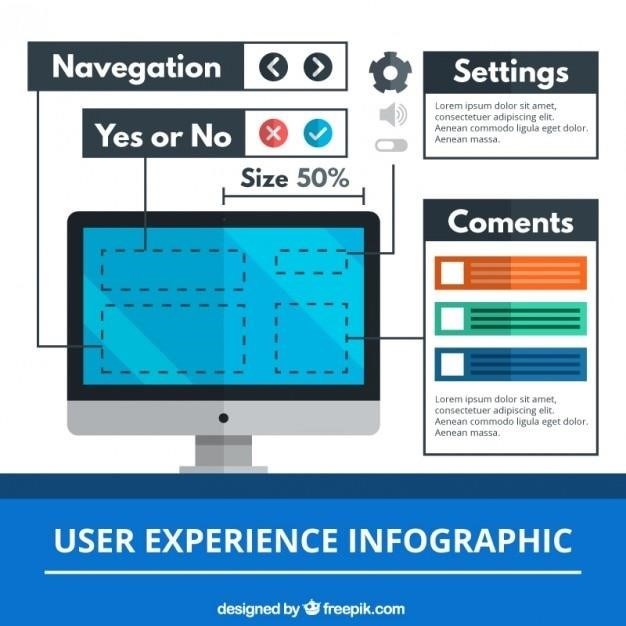
AS9100C⁚ A Comprehensive Guide to the Aerospace Quality Standard
What is AS9100C?
AS9100C is a widely recognized international quality management standard specifically designed for the aerospace industry. It outlines comprehensive requirements for organizations involved in the design, development, production, and maintenance of aerospace products and services. AS9100C builds upon the foundation of ISO 9001, incorporating additional requirements tailored to the unique demands of the aerospace sector.
What is AS9100C?
AS9100C is a globally recognized quality management standard specifically tailored for the aerospace industry. It’s a comprehensive set of guidelines that outline the requirements for organizations involved in the design, development, production, and maintenance of aerospace products and services. AS9100C acts as a robust framework, ensuring that organizations operating within the aerospace sector adhere to rigorous quality standards, fostering consistent product quality and safety throughout the supply chain. It’s based on the principles of ISO 9001, but with additional requirements that address the unique demands of the aerospace industry, making it a critical element in establishing a robust quality management system for aerospace organizations.
The Importance of AS9100C Certification
AS9100C certification is not merely a compliance requirement; it’s a strategic advantage for aerospace organizations. It serves as a powerful testament to a company’s commitment to quality, reliability, and safety. This certification signifies that an organization has implemented a comprehensive quality management system that meets the stringent demands of the aerospace industry. It provides assurance to customers, partners, and stakeholders that the company is committed to delivering products and services that meet the highest standards of safety and performance. AS9100C certification can enhance a company’s reputation, increase market competitiveness, and open doors to new opportunities within the aerospace sector, ultimately contributing to its success.
Key Requirements of AS9100C
AS9100C lays out a comprehensive framework for quality management, encompassing various critical elements. These requirements are designed to ensure that organizations consistently deliver products and services that meet customer expectations and industry standards. The standard emphasizes a process-oriented approach, focusing on the continuous improvement of processes and the identification and mitigation of risks. Key requirements include a robust quality management system, customer focus, strong leadership, effective engagement of personnel, evidence-based decision-making, and a commitment to continuous improvement. By adhering to these requirements, organizations can establish a culture of quality excellence, fostering customer satisfaction, operational efficiency, and long-term success in the aerospace industry.
Quality Management System
The cornerstone of AS9100C is the establishment of a robust Quality Management System (QMS). This system serves as a comprehensive framework for managing all aspects of an organization’s operations related to quality; The QMS encompasses documented procedures, processes, and responsibilities to ensure consistent product and service quality. It includes elements such as quality planning, control, assurance, and improvement. Organizations are required to document their QMS, making it readily accessible for internal and external audits; The QMS plays a vital role in achieving customer satisfaction, meeting regulatory requirements, and enhancing operational efficiency. By establishing a well-defined QMS, organizations demonstrate their commitment to quality excellence in the aerospace industry.
Customer Focus
AS9100C emphasizes a strong customer focus, recognizing that customer satisfaction is paramount in the aerospace industry. Organizations are expected to understand and meet the evolving needs and expectations of their customers. This includes actively seeking feedback, responding promptly to inquiries, and addressing any concerns or complaints effectively. Customer requirements are meticulously documented and integrated into all stages of the product or service lifecycle. The focus on customer satisfaction extends beyond simply meeting specifications; it encompasses building long-term relationships based on trust, reliability, and a commitment to delivering exceptional value. This customer-centric approach is essential for organizations to thrive in the highly competitive aerospace market.
Leadership
AS9100C places a strong emphasis on effective leadership, recognizing its crucial role in driving a successful quality management system. Top management is accountable for establishing and maintaining a quality policy that aligns with the organization’s strategic goals. This includes defining clear quality objectives, allocating necessary resources, and ensuring that the quality management system is effectively implemented and maintained. Leadership is also responsible for fostering a culture of continuous improvement, encouraging employee engagement, and promoting a commitment to meeting customer expectations. Strong leadership provides the foundation for a high-performing organization that consistently delivers products and services that meet the stringent demands of the aerospace industry.
Engagement of People
AS9100C emphasizes the importance of actively engaging people at all levels of the organization. This includes fostering a culture of open communication, collaboration, and empowerment. Employees are encouraged to contribute their ideas, expertise, and insights, playing a vital role in the continuous improvement of the quality management system. The standard promotes training and development opportunities to enhance employee skills and knowledge, creating a workforce that is both competent and motivated. By fostering a positive and supportive work environment, AS9100C aims to unlock the full potential of its workforce, driving innovation and excellence throughout the organization.
Process Approach
AS9100C promotes a process-oriented approach to quality management. This means that organizations are encouraged to identify, analyze, and manage their key processes in a systematic and structured manner. The standard emphasizes the importance of understanding the interrelationships between processes and how they contribute to the overall effectiveness of the quality management system. By adopting a process approach, organizations can optimize their operations, reduce waste, and improve efficiency. This includes identifying and managing risks associated with each process, ensuring that all activities are aligned with the organization’s quality objectives.
Evidence-Based Decision Making
AS9100C emphasizes the importance of making decisions based on objective evidence rather than assumptions or personal opinions. The standard encourages organizations to establish systems for collecting, analyzing, and interpreting data related to their quality management system. This data can include customer feedback, process performance metrics, and nonconformity reports. By using evidence-based decision making, organizations can ensure that their decisions are informed, sound, and aligned with their quality objectives. The standard also encourages organizations to document their decision-making processes to ensure transparency and accountability. This includes outlining the evidence considered, the rationale behind the decision, and the actions taken.
Relationship Management
AS9100C recognizes the critical role of strong relationships in the aerospace industry. The standard emphasizes the importance of establishing and maintaining effective relationships with customers, suppliers, and other stakeholders. Organizations are expected to clearly define their responsibilities and expectations for each relationship, ensuring that both parties understand their roles and obligations. The standard encourages organizations to build trust and transparency through open communication, timely information sharing, and collaborative problem-solving. It also emphasizes the importance of addressing issues promptly and fairly, fostering a spirit of mutual respect and understanding. By promoting effective relationship management, AS9100C helps organizations create a collaborative and supportive ecosystem within the aerospace industry.
Continuous Improvement
AS9100C emphasizes a commitment to ongoing improvement, recognizing that the aerospace industry is constantly evolving. The standard encourages organizations to establish a culture of continuous improvement, where every individual is empowered to identify and implement opportunities for enhancement. This includes actively seeking feedback from customers, suppliers, and employees to identify areas for improvement. Organizations are expected to implement a system for tracking, analyzing, and addressing non-conformances, ensuring that corrective and preventive actions are taken to prevent recurrence. AS9100C promotes a data-driven approach to improvement, encouraging organizations to collect and analyze performance data to identify trends and implement targeted initiatives. By fostering a culture of continuous improvement, AS9100C helps organizations stay competitive, meet evolving customer demands, and enhance their overall performance.
Benefits of Implementing AS9100C
Implementing AS9100C offers a multitude of benefits for aerospace organizations. It enhances customer satisfaction by consistently delivering high-quality products and services that meet or exceed expectations. AS9100C helps organizations optimize their processes, reducing waste and improving efficiency, leading to cost savings. The standard fosters a culture of continuous improvement, driving innovation and enhancing operational effectiveness. By demonstrating their commitment to quality through AS9100C certification, organizations gain a competitive advantage, increasing their credibility and attracting new customers. Furthermore, AS9100C helps organizations manage risks effectively, reducing the likelihood of defects and ensuring compliance with regulatory requirements. Overall, AS9100C implementation empowers organizations to achieve excellence in their operations and build a sustainable foundation for growth in the demanding aerospace industry.
How to Obtain AS9100C Certification
To obtain AS9100C certification, organizations must undergo a comprehensive process involving several key steps. First, they need to develop and implement a robust Quality Management System (QMS) that aligns with the requirements outlined in the AS9100C standard. This involves documenting processes, establishing procedures, and training personnel. Next, organizations must select a qualified certification body to conduct an independent audit of their QMS. The certification body will assess the organization’s compliance with AS9100C requirements and identify any areas for improvement. Following a successful audit, the certification body will issue a certificate confirming the organization’s compliance with AS9100C. Organizations must maintain their QMS and undergo regular audits to ensure ongoing compliance with the standard. Obtaining AS9100C certification requires a commitment to continuous improvement and adherence to the principles of quality management, ultimately demonstrating the organization’s dedication to delivering excellence in the aerospace industry.
Resources for AS9100C Implementation
Numerous resources are available to support organizations in their AS9100C implementation journey. The SAE International website provides access to the latest AS9100C standard, along with related publications and guidance documents. Industry associations, such as the International Aerospace Quality Group (IAQG), offer training programs, workshops, and webinars to assist organizations in understanding and implementing AS9100C requirements. Various consulting firms specialize in AS9100C implementation, providing expert guidance, audit support, and customized solutions tailored to specific organizational needs. Online platforms and forums dedicated to quality management provide a valuable resource for knowledge sharing, best practice exchange, and networking opportunities. Organizations can also access free resources, such as checklists, templates, and implementation guides, available online and through industry publications. Leveraging these resources can significantly enhance the effectiveness and efficiency of AS9100C implementation, ensuring a smooth transition to a compliant quality management system.