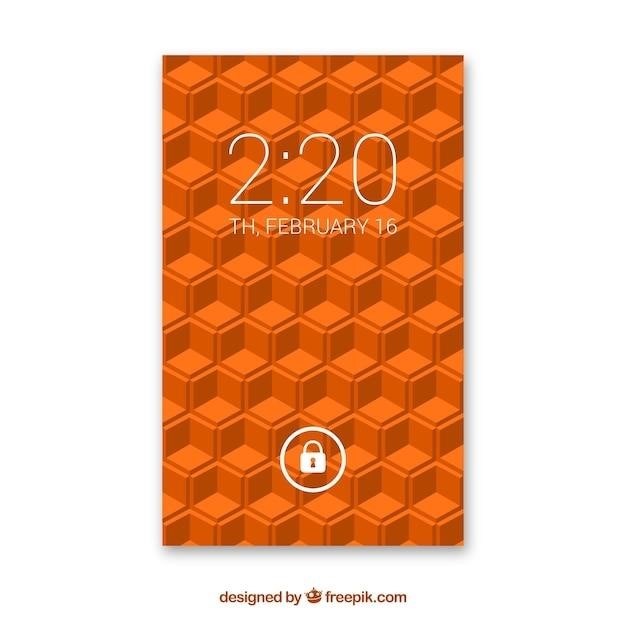
Millermatic 252 Manualā A Comprehensive Guide
This manual provides a comprehensive guide to the Millermatic 252, a versatile and powerful MIG welder designed for industrial and commercial applications. It covers everything from safety precautions and installation to welding parameters and troubleshooting, helping you get the most out of your machine.
Introduction
The Millermatic 252 is a versatile and powerful MIG welder designed for a wide range of industrial and commercial applications. It’s a robust and reliable machine capable of handling a variety of materials, including mild steel, stainless steel, and aluminum. Whether you’re a professional welder or a DIY enthusiast, the Millermatic 252 offers the power and precision needed to tackle challenging welding tasks.
This manual serves as a comprehensive guide to understanding and using the Millermatic 252 effectively. From safety precautions to welding parameters, troubleshooting, and maintenance, this manual provides all the information you need to operate the machine safely and efficiently.
Features and Specifications
The Millermatic 252 boasts a range of features designed for both efficiency and user-friendliness. It features a powerful 200 amp output, capable of welding up to 1/2-inch thick materials. The machine is also equipped with a built-in wire feeder, providing smooth and consistent wire feeding. The Millermatic 252 also incorporates a variety of user-friendly features, including a simple control panel and a clear digital display.
The Millermatic 252 is available in both 208/240 volt and 230/460/575 volt models. The 208/240 volt model has a maximum output of 250 amps at a 40% duty cycle, while the 230/460/575 volt model has a maximum output of 300 amps at a 40% duty cycle. The Millermatic 252 is also compatible with a variety of welding guns, including the MDX-250 MIG gun with AccuLock consumables for .030/.035 in. (0.8/0.9 mm) wire.
Safety Precautions
Welding is inherently dangerous, and the Millermatic 252 is no exception. It’s crucial to follow all safety precautions outlined in the manual to prevent injuries. Always wear appropriate personal protective equipment (PPE), including a welding helmet with a shade level appropriate for the welding process, heat-resistant gloves, and clothing that covers your entire body. Ensure proper ventilation when welding, as fumes and gases produced during welding can be harmful. Never weld on closed containers, as they can explode. Always use the correct compressed gas cylinders, regulators, hoses, and fittings designed for the specific application.
Always maintain equipment in good condition, including gas cylinders, regulators, hoses, and fittings. Never weld on a pressurized cylinder as it can cause an explosion. Be aware that electromagnetic energy from welding can interfere with sensitive electronic equipment. Locate welding operations 100 meters from any sensitive electronic equipment to minimize interference.
Installation and Setup
Proper installation and setup are essential for safe and effective operation of the Millermatic 252. The manual provides detailed instructions on selecting a suitable location, connecting input power, installing work cables, and connecting various components. When selecting a location, ensure the unit is stable and cannot tip over. Avoid areas where gasoline or volatile liquids are present, as this may require special installation procedures.
Connecting input power is a critical step, and the manual outlines the specific requirements for 208/240-volt and 460/575-volt models. Properly connecting the work cable to the negative output terminal is crucial for grounding and safety. The manual also details the steps for connecting Spoolmatic and XR Aluma-Pro guns, including proper polarity settings for different wire types. Installing the gas supply requires a secure connection to prevent cylinder leaks and accidents.
Selecting a Location
Choosing the right location for your Millermatic 252 is crucial for safe and efficient operation. The manual emphasizes the importance of selecting a stable and level surface to prevent the unit from tipping over. It also advises against placing the welder in areas where gasoline or volatile liquids are present, as this could pose a significant fire hazard. If operating in such environments, special installation procedures are required. The manual recommends consulting the National Electrical Code (NEC) Article 511 or the Canadian Electrical Code (CEC) Section 20 for guidance on specific installation requirements.
Additionally, the manual advises considering the proximity of sensitive electronic equipment, as electromagnetic energy from welding can interfere with their operation. To minimize potential interference, it recommends keeping weld cables as short as possible, close together, and down low, such as on the floor. The manual also suggests locating the welding operation at least 100 meters away from sensitive electronic equipment to ensure minimal interference.
Connecting Input Power
The Millermatic 252 requires a reliable power source to operate. The manual provides detailed instructions on how to connect the unit to the appropriate input power supply. It emphasizes the importance of using the correct voltage and amperage for your specific model, as improper connections could damage the welder or pose a safety hazard. The manual instructs users to verify the voltage rating of their Millermatic 252, which can be either 200/240 volts or 230/460/575 volts. This information is crucial for selecting the appropriate power source and ensuring a safe and efficient connection.
The manual also provides detailed instructions on how to connect the power cord to the welder. It advises users to use a heavy-duty power cord with the correct amperage rating for their Millermatic 252 model. The manual also recommends using a dedicated circuit for the welder to ensure adequate power supply and prevent overloading other circuits.
Installing Work Cable and Clamp
The Millermatic 252 manual provides step-by-step instructions on how to install the work cable and clamp, which are essential for grounding the welding circuit and ensuring a safe and stable connection. The manual emphasizes the importance of using the correct cable size and length to minimize voltage drop and ensure adequate current flow. It also details the proper procedure for connecting the work cable to the negative (-) output terminal of the welder, ensuring a secure connection that will not easily detach during welding.
The manual then explains how to attach the work clamp to the workpiece, emphasizing the importance of choosing a clean and solid contact point to minimize resistance and ensure a good electrical connection. The manual also provides tips for ensuring a secure clamp connection, such as using a clamp with a strong spring and tightening it firmly to the workpiece. The manual highlights the importance of maintaining a short work cable to minimize voltage drop and ensure optimal welding performance.
Connecting Spoolmatic
The Millermatic 252 manual provides clear instructions on how to connect the Spoolmatic wire feeder, a crucial component for feeding welding wire to the welding gun. It outlines the connection process for both 15A and 30A guns, ensuring a secure and reliable connection. The manual advises users to carefully route the weld cable through the designated opening on the front panel to avoid any potential damage or interference with other components. It also emphasizes the importance of securely connecting the shielding gas hose to the Spoolmatic, ensuring a continuous flow of shielding gas during the welding process.
The manual includes illustrations and detailed descriptions, making the connection process straightforward. It also highlights the importance of ensuring a tight connection between the gun trigger plug and the receptacle on the Spoolmatic to guarantee a smooth and consistent wire feeding operation. The manual advises users to always check for any loose connections or potential hazards before starting the welding process, ensuring a safe and efficient operation.
Connecting XR Aluma-Pro, XR Aluma-Pro Lite, XR Edge, XR-A Gun, or XR-A Python
The Millermatic 252 manual provides comprehensive instructions on connecting various Miller welding guns, including the XR Aluma-Pro, XR Aluma-Pro Lite, XR Edge, XR-A Gun, and XR-A Python. The manual emphasizes the importance of using the correct adapter cord for XR Edge guns prior to serial number LE079101, ensuring a proper connection and optimal performance. It guides users through a step-by-step process, outlining the connection points on the gun and the welding machine. The manual provides clear illustrations and detailed explanations, making the connection process easy to understand and follow.
The manual also highlights the importance of ensuring a secure connection between the gun liner and the wire outlet guide, preventing any potential wire feeding issues. It advises users to carefully route the gun liner and wire outlet guide through the designated openings on the welding machine, ensuring a smooth and efficient flow of welding wire. The manual also emphasizes the importance of following the manufacturer’s instructions for each specific gun model, ensuring proper connection and safe operation;
Setting Gun Polarity for Wire Type
The Millermatic 252 manual emphasizes the importance of correctly setting the gun polarity based on the type of welding wire being used. It provides clear instructions and diagrams to guide users through the process, ensuring a safe and efficient welding experience. The manual highlights the importance of consulting the manufacturer’s recommendations for specific welding wire types, as different materials require different polarities for optimal performance.
The manual explains the difference between electrode positive (DCEP) and electrode negative (DCEN) polarities and the types of welding wires that are suitable for each. It clarifies that electrode positive (DCEP) is the standard polarity for welding solid steel, stainless steel, aluminum, or flux core with gas wires (GMAW). The manual also includes a visual representation of the polarity changeover label, highlighting the connections for the wire drive assembly lead, work clamp lead, negative terminal, and positive terminal, making the setting process straightforward.
Installing Gas Supply
The Millermatic 252 manual provides step-by-step instructions for installing the gas supply, ensuring a safe and secure connection. It emphasizes the importance of obtaining a gas cylinder and securing it to the running gear, wall, or another stationary support to prevent it from falling and breaking the valve. This prevents potential accidents and ensures a reliable gas flow for welding. The manual then guides users through the process of removing the cap from the cylinder valve, standing to the side of the valve, and opening it slightly to release any trapped air or impurities.
It also highlights the importance of using only correct compressed gas cylinders, regulators, hoses, and fittings designed for the specific application, ensuring compatibility and safety. The manual stresses the need to maintain these components in good condition, as damaged parts can pose significant risks. It also cautions against welding on pressurized cylinders, as this can lead to an explosion. The manual concludes this section by reminding users to handle compressed gas cylinders with care, as they contain gas under high pressure.
Installing Wire Spool and Adjusting Hub Tension
The Millermatic 252 manual provides detailed instructions for installing a wire spool and adjusting the hub tension, ensuring smooth and consistent wire feeding during welding. It starts by explaining how to hand-tighten the knob clockwise until a slight force is needed to turn the spool, indicating the correct tension. The manual then guides users through the process of installing either a 1lb or 2lb wire spool, using illustrations to clarify each step. It emphasizes the importance of selecting the appropriate wire spool size for the welding project, ensuring optimal performance and minimizing wire feed issues.
The manual goes on to explain how to adjust the hub tension, which is crucial for preventing wire feed problems. It highlights that excessive tension can cause the wire to break, while insufficient tension can lead to wire slippage and inconsistent feeding. The manual advises users to adjust the tension until the wire feeds smoothly and without any resistance, ensuring consistent and reliable welding performance.
Welding Parameters and Settings
The Millermatic 252 manual provides a comprehensive guide to understanding and adjusting welding parameters and settings, ensuring optimal welding performance for various materials and applications. It covers key settings such as wire feed speed, voltage, gas flow rate, and polarity, explaining their individual roles and how they interact to influence the welding process. The manual emphasizes the importance of selecting appropriate settings based on the specific welding application, material thickness, and desired weld quality.
The manual provides detailed information on wire feed speed, explaining how it affects the amount of wire delivered to the weld pool. It explains how to adjust the speed based on the material thickness, wire diameter, and desired weld bead size. Similarly, the manual discusses voltage, highlighting its impact on the arc length and penetration depth. It provides guidance on selecting the optimal voltage range based on the material type, thickness, and desired weld characteristics.
Wire Feed Speed
The Millermatic 252 manual provides detailed information on wire feed speed, a crucial parameter that dictates the amount of wire delivered to the weld pool per unit of time. The manual emphasizes the importance of setting the wire feed speed appropriately based on the material thickness, wire diameter, and desired weld bead size. It explains that a higher wire feed speed results in a faster deposition rate, leading to a larger weld bead and potentially a less penetrating weld.
Conversely, a lower wire feed speed results in a slower deposition rate, producing a smaller weld bead with potentially greater penetration. The manual offers a table of recommended wire feed speeds for various material thicknesses and wire diameters, helping users select the optimal setting for their specific welding application.
Voltage
The Millermatic 252 manual provides detailed information on voltage, a critical parameter that influences the welding arc characteristics and weld bead penetration. The manual explains that voltage is the electrical potential difference between the electrode and the workpiece, and it directly affects the arc length and heat input. Higher voltage results in a longer arc length and higher heat input, leading to a wider and shallower weld bead with potentially less penetration.
Conversely, lower voltage results in a shorter arc length and lower heat input, leading to a narrower and deeper weld bead with potentially greater penetration. The manual offers a table of recommended voltage settings for different welding applications, helping users select the optimal setting based on the material thickness, wire diameter, and desired weld bead characteristics.
Gas Flow Rate
The Millermatic 252 manual emphasizes the crucial role of gas flow rate in achieving optimal welding performance. The manual explains that the gas flow rate directly affects the shielding gas’s ability to protect the welding arc from atmospheric contamination, ensuring a clean and stable arc. An insufficient gas flow rate can lead to arc instability, spatter, and porosity in the weld bead, compromising the weld’s quality.
The manual provides a detailed explanation of how to adjust the gas flow rate using the regulator and flowmeter, highlighting the importance of maintaining a consistent flow rate throughout the welding process. It also discusses the different types of shielding gases commonly used with the Millermatic 252, including argon, carbon dioxide, and gas mixtures, and their respective flow rate recommendations for various welding applications.